Patented Technology
Introduction to Our Patented Technologies
GD Environmental proudly offers three cutting-edge patented technologies designed to revolutionize waste management and resource recovery. These technologies ensure environmentally sustainable solutions while maximizing cost efficiency and value creation.
1. Tri Fusion Dryer with Gasification & Pyrolysis Technology
This state-of-the-art patented technology provides a comprehensive solution for the disposal of Municipal Solid Waste (MSW) and Reject Waste. By combining drying, gasification, and pyrolysis processes, it achieves near-zero landfill dependency and pollution.
Key Features:
Complete Waste Processing: Handles mixed MSW and reject waste with 50% moisture and varying compositions.
Sustainability: Converts waste into high-value byproducts such as Green Coal, Syngas, and Fly Ash, aligning with the Waste to Wealth initiative.
Environmental Compliance: Validated under the Waste to Wealth Mission by the Principal Scientific Adviser (PSA), Government of India, ensuring adherence to strict environmental standards.
Applications: Ideal for decentralized waste management systems with a focus on circular economy principles.
Advantages:
- 100% waste disposal with no residual landfill.
- Production of high-calorific-value Green Coal and Syngas for energy applications.
- Fly Ash repurposed for eco-friendly construction materials.
2. Dual Fusion Dryer with Gasification Technology
This innovation is a cost-effective adaptation of the comprehensive system above, designed to lower capital expenditure (CapEx) without compromising efficiency.
Process:
- The system begins with drying MSW and reject waste in the Dual Fusion Dryer, reducing moisture content significantly.
- The dried waste, also known as Refuse-Derived Fuel (RDF), is then processed directly in the gasifier.
- By bypassing the pyrolysis stage, the system reduces the complexity and cost of installation and operation.
Key Features:
- Cost Efficiency: Eliminates the need for the pyrolysis chamber, reducing while maintaining high waste processing efficiency.
- Sustainability: Converts dried RDF into Green Coal and Syngas, ensuring a self-sustaining energy model.
- Compact Design: Requires less space and infrastructure compared to the full Tri Fusion Dryer with Pyrolysis setup.
Applications:
- Municipalities and small-scale waste processors seeking affordable yet efficient waste disposal solutions.
- Areas with limited budgets or space constraints.
3. Plastic to Pyrolysis Technology
This patented system addresses the challenge of plastic waste, particularly polystyrene, by converting it into high-value fuels and solvents.
Process:
Plastic Conversion: Processes various types of plastic and polystyrene to produce Pyrolysis Solvent Oil, a versatile byproduct.
Byproduct Utilization:
- The Solvent Oil is reused to dissolve polystyrene, enabling further processing.
- Through advanced refinement, the Solvent Oil is converted into high-quality Bharat Stage (BS) VI diesel.
Key Features:
- High-Value Output: Produces diesel compliant with BS VI standards, meeting modern emission norms.
- Self-Sustaining System: Utilizes byproducts within the process, minimizing waste and maximizing efficiency.
- Scalable and Versatile: Suitable for both centralized and decentralized setups.
Applications:
- Industries and municipalities seeking solutions for plastic waste management.
- Production of eco-friendly diesel from plastic waste.
Our patented technologies offer scalable, sustainable, and cost-effective solutions for modern waste management challenges.
The Tri Fusion Dryer with Gasification & Pyrolysis Technology delivers complete waste-to-energy transformation, making it the ultimate choice for comprehensive waste disposal.
The Dual Fusion Dryer with Gasification Technology offers an affordable alternative, focusing on drying and gasification to ensure effective waste disposal with lower Capital Expenditure.
The Plastic to Pyrolysis Technology efficiently processes plastic waste into high-quality fuel, contributing to the circular economy and reducing reliance on fossil fuels.
These technologies reflect our commitment to innovation, environmental sustainability, and economic feasibility, ensuring a cleaner and greener future for all.
Process of Tri Fusion Dryer with Gasification & Pyrolysis Technology Explained
Inert, Reject, Mixed, Dry, Wet Waste Disposal Project. Detailed Process of the Tri Fusion Dryer with Gasification & Pyrolysis Technology.
This state-of-the-art patented system seamlessly integrates gasification and pyrolysis technologies to process Municipal Solid Waste, MSW. It is designed to handle waste with a moisture content from 50% to 70% and a bulk density of 450 kg per cubic meter, for mixed waste, 800 kg per cubic meter for wet waste and 90 kg per cubic meter for dry waste, converting it into clean energy and sustainable products.
Process Overview:
The process begins with the patented gasifier ignited using fuel pellets, bio coal, wood and up to 5% refuse derived fuel, RDF. This initial step ensures a stable heat source to power the system.
Municipal solid waste is unloaded from garbage trucks onto a conveyor system.
From here, the waste is directed to a shredder, via a Hopper for pretreatment, reducing its size and preparing it for drying.
The shredded waste is conveyed into a rotary drum dryer maintained at a constant temperature of 90o degrees Celsius achieved using heat from the gasifier. Here, the moisture content of the waste is significantly reduced from 50% to a dried mass.
The extracted moisture, along with any volatiles in vapor form, is channeled to a thermal oxidizer. This ensures safe, efficient, and environmentally compliant disposal.
The dried mass is then fed into the patented pyrolysis chamber, where it undergoes thermal decomposition in the absence of oxygen. When heated to a temperature of 350 degrees Celsius, this process produces Green Coal—a high-calorific-value byproduct that serves as an efficient fuel source. Alternatively, if heated to 700 degrees Celsius, the gas is extracted from the coal to produce Syngas, leaving behind brittle carbon with no calorific value.
In a decentralized setup, gasification combined with a rotary drum dryer is typically employed for preliminary treatment. This process dries the waste to create RDF, which can then be transported to a central location for further processing—either to generate gas or coal, depending on market demand. Additionally, this preliminary treatment leads to a 70% reduction in waste volume, significantly facilitating easier and more cost-effective transport.
The produced green coal is used as an input for the gasifier, making the system self-sustaining by generating the energy required to power itself. This closed-loop design eliminates dependency on external energy sources.
- During gasification, fly ash, a byproduct constituting about 5% of the input, is collected. Instead of disposing of it, this ash is combined with crushed sand, cement, and other materials to produce eco-friendly paving blocks and bricks.
- This promotes sustainable construction practices.
- The process is designed to leave no residual waste for landfill disposal, as all materials are converted into value-added products.
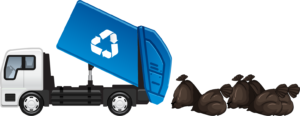
Initial MSW Handling
Municipal Solid Waste is unloaded from Garbage Trucks onto a Conveyor System.
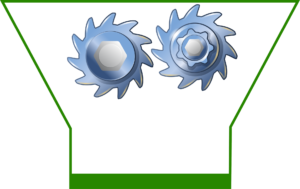
Hopper Loading
Waste passes through a hopper to a shredder for pretreatment, reducing size before drying.
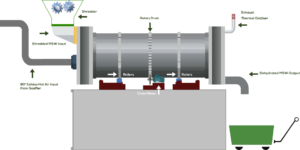
Transfer to Rotary Dryer
Shredded waste is fed into a drum dryer maintained at 90°C using gasifier heat, reducing moisture content from 50% to a dry, processable form. This enhances efficiency for downstream conversion.
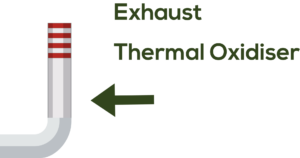
Thermal Oxidation
Moisture and volatile vapors are sent to a thermal oxidizer for safe and compliant disposal.
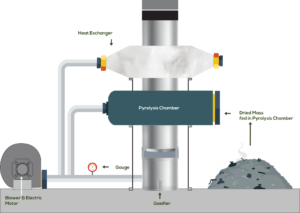
Transfer to Patented Pyrolysis Chamber
Dried waste enters a patented pyrolysis chamber for thermal decomposition. At 350°C, it produces Green Coal; at 700°C, Syngas and inert carbon.
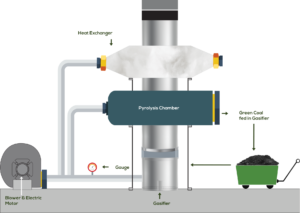
Transfer to Patented Gasifier
Green coal powers the gasifier, creating a self-sustaining, closed-loop system that runs without external energy.
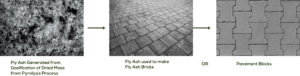
Fly Ash Generation
Fly Ash from Gasification (≈5% of input) is repurposed with Sand & Cement to create Eco-friendly Bricks & Pavers, supporting Sustainable Construction.
Key Features of the Dual Fusion Dryer Technology:
- Make in India Technology / Solution
- Online Monitoring System
- Odor-Free and Leachate-Free Operations
- Self – Sustaining Process
- Minimal Space Requirements
- Zero Hazardous Emissions
- Quick Results with Valuable Byproducts
The Tri Fusion Dryer with Gasification & Pyrolysis Technology and Plastic to Pyrolysis Technology are 100% Make in India innovations, developed to revolutionize waste management and resource recovery in the country. These technologies align with the Atmanirbhar Bharat initiative, offering sustainable and cost-effective solutions tailored to India’s unique waste challenges.
Key Highlights:
- Indigenous Design and Manufacturing: Entirely designed, developed, and manufactured in India, promoting local industries and expertise.
- Tailored for India’s Needs: Optimized to handle India’s diverse municipal solid waste (MSW) and plastic waste streams, ensuring maximum efficiency.
- Sustainable Solutions:
- Tri Fusion Dryer with Gasification & Pyrolysis Technology: Achieves near-zero landfill and pollution while producing valuable byproducts like Green Coal, Syngas, and Fly Ash Bricks.
- Plastic to Pyrolysis Technology: Converts plastic waste into high-quality Bharat Stage (BS) VI diesel, promoting circular economy practices.
- Economic Viability: Cost-effective and scalable models designed for municipalities, startups, and entrepreneurs.
- Environmental Compliance: Validated under the Waste to Wealth Mission by the Principal Scientific Adviser, Government of India, ensuring adherence to the highest environmental standards.
These Make in India technologies showcase the potential of indigenous innovation to solve global challenges while empowering local economies and advancing sustainability.
With an advanced online monitoring system, our technology ensures seamless, real-time tracking of the entire waste disposal process—efficient, reliable, and systematic
Say goodbye to unpleasant odors, bad smells, and harmful leachate. Our innovative Thermal Oxidizer system creates a clean, odor-free environment, protecting the community and ecosystem
Our system is fully self-sustaining, requiring no external energy input to power the waste disposal process. It’s efficient, eco-friendly, and cost-effective!
With a compact design, our technology requires significantly less space than traditional waste management solutions—perfect for urban and decentralized setups
Prioritizing environmental safety, our system ensures zero emissions of hazardous gases, meeting and exceeding global standards.
Why wait for months? With quick results, our process efficiently transforms waste into valuable byproducts, contributing to a circular economy.
Benefits:
The Tri Fusion Dryer with Gasification & Pyrolysis Technology offers multiple benefits, reduces legacy landfill dependency, generates clean energy, creates eco-friendly construction materials like fly ash bricks, complies with stringent environmental standards.
Aligns with the CPCB Guidelines:
Tri-Fusion Dryer with gasification and pyrolysis technology represents a breakthrough in waste management, turning MSW into valuable resources while protecting the environment.
Our innovative Tri Fusion Dryer with Gasification and Pyrolysis Technology aligns closely with the Municipal Solid Waste (MSW) selection criteria outlined in CPCB guidelines. By efficiently reducing moisture content to <10-12%, our technology enhances the calorific value of waste, making it ideal for thermal processes like gasification and pyrolysis. It ensures compliance with environmental norms by minimizing emissions and maximizing resource recovery in the form of syngas and Green Coal. Additionally, it supports scalability, offering a sustainable solution for varied waste quantities, from decentralized small-scale setups to large integrated plants. Please refer to the chart provided below.

Key By-Products:
The Tri Fusion Dryer with Gasification & Pyrolysis Technology is designed not just for waste disposal but also for the efficient recovery of valuable byproducts. Each byproduct serves a specific purpose, contributing to environmental sustainability and resource conservation. Below is a detailed explanation of the key byproducts:
- Hot Air and Hot Water
- Biochar
- Green Coal
- Sty Paint
- Fly Ash Bricks
- Fuel Pellets
- Hot Air: The gasification and pyrolysis processes generate significant amounts of hot air, which can be harnessed for various industrial applications. This hot air can be used directly in processes that require thermal energy, such as drying, heating, or even generating electricity through steam turbines.
- Hot Water: The heat produced during the waste conversion process can also be used to heat water. This hot water can serve multiple purposes, including industrial heating, space heating, and domestic use. It can also be used in combined heat and power (CHP) systems to maximize energy efficiency.
- Definition and Production: Biochar is a stable, carbon-rich material produced from the pyrolysis of organic waste. It is a highly porous substance that retains many of the properties of the original biomass but in a more stable form.
- Applications: Biochar has several environmental benefits. When applied to soil, it improves soil fertility, water retention, and nutrient availability. It also acts as a long-term carbon sequestration agent, helping to mitigate climate change by locking carbon in the soil for centuries. Additionally, biochar can be used in water filtration and as an additive in animal feed to improve digestion and reduce methane emissions.
- Definition and Production: Green Coal is produced by the gasification and pyrolysis of organic waste materials. It is a cleaner-burning alternative to conventional fossil coal, with lower emissions of sulfur dioxide (SO₂), nitrogen oxides (NOx), and particulate matter.
- Applications: Green Coal can be used as a substitute for traditional coal in industrial boilers, power plants, and other applications requiring solid fuel. It offers a more sustainable energy option, reducing the reliance on fossil fuels and lowering the carbon footprint of energy-intensive industries.
- Definition and Production: Sty Paint is a byproduct derived from the processing of waste materials. It is formulated for external use, particularly in applications where durability and environmental resistance are essential.
- Applications: This paint can be used for coating and protecting external surfaces such as walls, fences, and other structures. It provides a sustainable alternative to conventional paints, utilizing recycled materials and contributing to waste reduction.
- Definition and Production: Fly ash, a byproduct of the gasification process, is a fine, powdery material that can be combined with other binders to produce fly ash bricks. These bricks are made by compressing the mixture into molds and then curing them under controlled conditions.
- Applications: Fly ash bricks are an eco-friendly building material that can be used in construction for paving, cladding, and wall building. They offer several advantages over traditional clay bricks, including better strength, reduced water absorption, and lower environmental impact. By using fly ash in brick production, the process diverts waste from landfills and reduces the need for virgin materials.
- Definition and Production: Fuel Pellets are small, cylindrical pieces of compressed organic material, typically made from the residues of waste processing. These pellets are dense, easy to store, and transport, and they have a high energy content.
- Applications: Fuel pellets serve as a renewable energy source for heating systems, power generation, and industrial processes. They can be used in pellet stoves, boilers, and power plants designed to burn biomass. The use of fuel pellets helps reduce dependence on fossil fuels, lowers greenhouse gas emissions, and promotes the utilization of renewable energy sources.
These byproducts from the Tri Fusion Dryer with Gasification & Pyrolysis Technology are not only valuable in their own right but also represent a significant step towards sustainable waste management and resource recovery. By transforming waste into useful products, GDEPL’s technology supports a circular economy, where resources are continually reused and recycled, minimizing environmental impact and promoting sustainability.
Patented Plastic Pyrolysis Technology
GDEPL’s Patented Plastic Pyrolysis Technology offers an innovative and sustainable solution to the global challenge of plastic waste. This technology is specifically designed to process legacy landfill plastics, including complex polymers such as polystyrene and polypropylene, converting them into oil (fuel) equivalent to Bharat Stage VI diesel, one of the highest emissions standards in the world.
The Patented Plastic Pyrolysis Technology is an innovative and sustainable solution for converting waste plastic into valuable crude oil and other byproducts. This process, known as depolymerization, breaks down plastic polymers into smaller hydrocarbon molecules, effectively turning them back into oil. The technology is designed to handle various types of plastics, each requiring specific treatment methods based on its chemical properties.
Process Overview:
- Polypropylene (PP): This type of plastic is relatively straightforward to process as it does not have a tendency to form wax. It can be easily converted into oil without the need for additional catalysts.
- Polyethylene (PE): Unlike PP, polyethylene has a tendency to form wax, which requires the use of suitable catalysts to facilitate the conversion process and prevent the formation of unwanted byproducts.
- Polystyrene (PS) (Thermocol): Polystyrene yields high-quality oil, but its low density makes transportation expensive. To overcome this, GDEPL has developed a proprietary closed-loop system that processes polystyrene efficiently.
- GDEPL’s closed-loop system is designed to maximize efficiency and minimize waste. The company operates on a business model that involves charging waste generators for processing their plastic waste. GDEPL does not purchase plastic; instead, it processes plastic waste that is brought to its collection centers, typically as part of municipal solid waste or through industrial clients who require segregation and processing services.
- Collection and Segregation: GDEPL offers plastic processing services to clients, focusing on plastics that have no commercial value and require segregation. Waste plastic is collected, segregated, and prepared for processing at GDEPL’s facilities.
- Melting and Conversion: The plastic waste is melted using fuel generated from the waste-to-oil process. Flexible plastics are melted into blocks, which are then brought to the pyrolysis plant for conversion into oil. Polystyrene is treated with a proprietary solvent to create a semisolid melt that is also processed into oil at the pyrolysis plant.
- GDEPL has achieved a high level of expertise in processing waste plastic into drop-in fuel. This fuel is equivalent to high-speed diesel and meets Bharat VI specifications, making it suitable for use in vehicles and machinery. GDEPL’s industrial waste generators are also customers for this drop-in fuel, which they use directly in gensets and other applications.
Key By-Products:
The Tri Fusion Reactor Gasifier Technology is designed not just for waste disposal but also for the efficient recovery of valuable byproducts. Each byproduct serves a specific purpose, contributing to environmental sustainability and resource conservation. Below is a detailed explanation of the key byproducts:
- Drop-in-Fuel
- Biochar
- Sty Paint
- Definition and Use: The primary product of the pyrolysis process, drop-in-fuel is equivalent to Bharat Stage VI diesel. It is a high-quality fuel that can be used in vehicles, machinery, and gensets, reducing reliance on traditional fossil fuels. This fuel is a cleaner alternative, contributing to lower emissions and a reduced environmental footprint.
- Definition and Production: Biochar is a stable, carbon-rich material produced from the pyrolysis of organic waste. It is a highly porous substance that retains many of the properties of the original biomass but in a more stable form.
- Applications: Biochar has several environmental benefits. When applied to soil, it improves soil fertility, water retention, and nutrient availability. It also acts as a long-term carbon sequestration agent, helping to mitigate climate change by locking carbon in the soil for centuries. Additionally, biochar can be used in water filtration and as an additive in animal feed to improve digestion and reduce methane emissions.
- Definition and Use: Derived from the processing of specific types of plastics, Sty Paint is a byproduct used for external applications and water-proofing solutions. It offers a sustainable alternative to conventional paints, utilizing recycled materials and contributing to the reduction of plastic waste.
The Patented Plastic Pyrolysis Technology developed by GDEPL not only addresses the challenge of plastic waste management but also creates valuable products that can be reintegrated into the economy. By converting waste plastic into high-quality fuel and other byproducts, this technology supports the principles of a circular economy, where waste is minimized, and resources are continually reused. GDEPL’s approach is a testament to the potential of innovative technologies to create sustainable solutions for some of the most pressing environmental issues of our time.